Immersion Heater Protection
Applications:
Immersion Heater Burn-Out Protection
Immersion Heater Overheat Protection
Application Background:
Immersion heaters are widely used in various industries where tanks, vats, and other vessels are needed to provide an elevated temperature change in the production process. Examples include heating a chemical bath in a plating operation, annealing of metal parts, and even deep frying of potato chips.
The problem comes when the level of the fluid in the vessel (oil, water, etc.) drops below the heater and allows the heater to rise above normal operating temperatures. This typically would cause the heater element to burn-out and in some cases create a severe and hazardous situation.
Application Solution:
There are many fluid level switch technologies including: sight glass, conductivity probes, floats, capacitance probes, etc. All have proven to work with varying degrees of success. Some rely on operator’s attention and memory. Some have mechanical parts and prone to wear and failure. Still other electronic type probes require conducting fluids or fluids of different capacitance.
A better solution for the interface detection is the Thermal Differential Switch. The TD Switch has two thermal sensing devices (RTD’s) encased in miniature stainless steel probes. One sensor detects the temperature of the fluid while the second has a small current applied to create a thermal differential temperature above the fluid temperature. The differential temperatures created between the probe in air and the probe in a liquid is different. Therefore detection of a near uncovered heater is achieved reliably, with excellent repeatability.
With a single process connection into the vessel either through the side (horizontally) or through the top (vertically) a TD probe is strategically located to optimize the point at which the heater becomes almost uncovered by the fluid. With the dual channel VersaSwitch® product from Delta M Corporation it is easy set one switch channel for the fluid level and the second switch channel for a maximum temperature set point. Separate relays activate depending upon whether the sensor probe is uncovered from the fluid or if the temperature has exceeded a safe set point.

to learn how to set the second channel of a Dual Channel Level Switch to react to a temperature set-point.
Recommended Products:
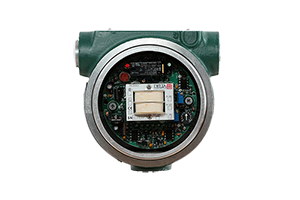
Reactor/Vessel Charging - Tank Leak Detection
- CSA, Ex, CE, CENELEC, 3A, NEMA4x
- Choose 110VAC, 220VAC or 24VDC Electronics
- Multi-Point and Shrouded Options
- Available in SS, Hastelloy, Titanium & More
- Uniquely Welded Sensor Designs
- Quick Response Time
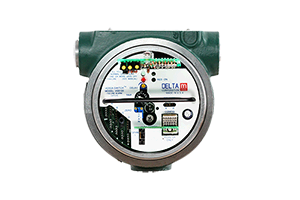
w/ Unit Diagnostics
Safety Relief Valve Monitor - Soot Blower Feed Water Monitor
Rotating Equipment Lubrication - Vapor Recovery Monitor
Gas Booster Monitor - Food & Beverage Liquid Flow Monitor
- User Selectable Power – 110/220VAC/24VDC
- Optional Remote Electronics for easy setup
- Nearly any Process Connection - Custom or Common
- Wide operating temperature range up to 850F
- 2nd Channel for Detection of Unit Diagnostics
- Two year workmanship warranty